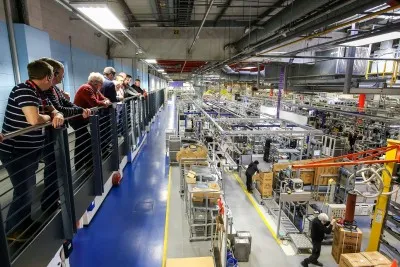
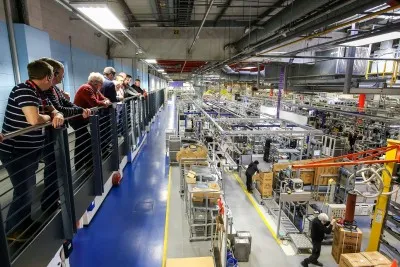
Worcester, Bosch Group, has redesigned its factory tour, giving installers the opportunity to get even more of the VIP treatment, while they discover what it takes to manufacture the boilers it regularly fits.
With over 400 process steps and 600 parts required to produce a typical Worcester appliance, the new tour has been designed so installers, specifiers and merchants can observe the level of care and rigorous testing that is carried out on all of its leading products.
Tours will be conducted by one of the manufacturer’s expert Technical Trainers, who are able to field any questions that may arise as visitors make their way around the factory, providing an altogether more interactive experience.
Offering more access than ever before, the new route covers all key areas and takes visitors along the four lean assembly lines designed to cope with seasonal customer demand. Visitors will gain insight into the heat exchanger build, copper shop, press shop, paint shop, sub-assembly line as well as the quality-testing department.
At each section, an area expert will present a practical overview, demonstrating the level of skill involved in producing every Worcester boiler. Every department also includes dedicated viewing areas, with designated ‘selfie’ points giving engineers the chance to share their best #WorcesterSelfie on social media.
In the afternoon, guests take part in a thorough product training session, where they will have time to get hands-on with the latest models and technologies, and experience the personal development sessions offered by Worcester.
At the end of their day, visitors will receive a Worcester jacket and an exclusive cash-back voucher to take home, along with a greater understanding of the detail and precision that goes into making every Worcester product.
To find out more about signing up to one of Worcester’s new factory and facilities tours, register your interest at: worcester-bosch.co.uk/factory