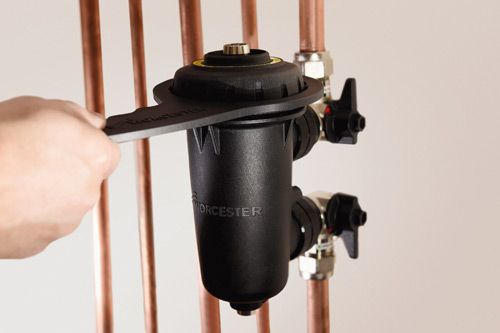
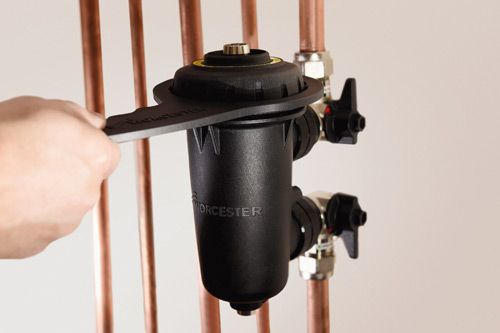
Flushing out a system before installing a replacement boiler is a mandatory requirement under the UK’s 2005 Building Regulations, but new systems can also benefit highly from this practice. Martyn Bridges, director of technical communication and product management at Worcester, Bosch Group, divulges his top tips for successful heating system water treatment.
1. DO keep your objectives in mind at all times. Water treatment should be seen as compulsory for any new boiler installation, as well as replacements. A successful water treatment procedure will reduce the likelihood of corrosion to system metals and prevent contaminants from forming, such as sludge, scale, or microbiological organisms. Overall, water treatment ensures that the system performs to its design specification for as long as possible. By being aware of this, you can maintain a standard of best practice, while reassuring the customer that any initial costs will be worth it in the long-term.
2. DO survey the system before starting a cleansing or flushing procedure. A full examination will help you to identify any radiators that are not working properly, as well as any hidden areas of the system that will need to be considered. You will also get a better idea of the volume and general condition of the heating system, which will ensure that you use the most beneficial water treatment procedure possible.
3. DO follow British Standard 7593. This is the code of practice for the treatment of water in domestic hot water central heating systems, and states that you must fit a corrosion inhibitor to all wet central heating systems when the system is filled. In addition to this, you need to flush any new systems with a chemical cleaner, which will remove installation debris and flux residues. If you’re working with an older system, flush it with a cleanser using powered assistance, which will remove sludge prior to boiler replacement.
4. DO use a system filter. There’s a wide range available, and each one will have its advantages and disadvantages, depending on the heating system you’re working with. A twin-action system filter, for example, captures both magnetic and non-magnetic system contaminants. These products are relatively low-cost, but they can reap significant savings by increasing boiler efficiency and keeping energy costs down.
5. DO test the turbidity of the water. This is a simple way of checking how clean a system is, by using a turbidity tube to monitor discharge water and make sure that it has been cleared successfully during the power flushing process. This helps installers to demonstrate to customers just how contaminated a system might be, providing a good incentive for homeowners to make water treatment a regular maintenance procedure for their heating systems.
6. DON’T ignore its value. It’s tempting for both installers and homeowners to see system water treatment as an optional extra, particularly for new installations, but the benefits always outweigh the initial costs. Make sure your customer is aware of all the advantages a successful water treatment procedure can bring, such as enhanced boiler efficiency and lower bills. They’ll certainly thank you for it later.
7. DON’T overuse certain materials when installing a boiler. Flux, oils and grease are useful materials for an installation, but they are also some of the most common contaminants found after a thorough filtration process. If left unchecked, these contaminants could eventually reduce the boiler’s performance, so use them sparingly.
8. DON’T forget the radiators. Radiators are a huge part of a system’s overall efficiency, yet they often play second fiddle to the boiler when it comes to installations and repairs. Cold spots are one of the most regular occurrences, and can be fixed simply by bleeding the radiator. To save your customer the trouble of a call-out, make sure that you demonstrate this procedure during a new boiler installation. This will also reduce the risk of hydrogen build-up as a result of system corrosion.